Tariffs aren’t enough to reshore apparel manufacturing
Trump insists tariffs will help bring back domestic manufacturing. But for industries like apparel, things aren’t so simple.
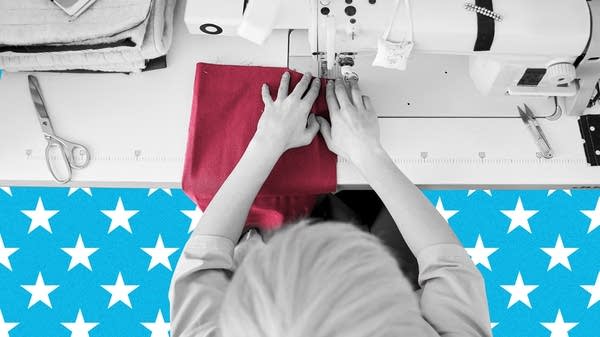
This month, President Donald Trump announced sweeping tariffs on imports to the U.S. – a base tariff of 10% on April 2 and target tariffs on various countries that took effect April 9 but were paused for 90 days some hours later.
Among these countries are China, Vietnam, Bangladesh, Indonesia, India, Cambodia and Pakistan — countries that account for 66% of apparel imports to the U.S.
These import taxes, which range from 145% for China to 27% for India, were proposed with the goal of bringing back jobs and manufacturing to the U.S., according to the administration.
But for some industries, such as apparel, reshoring will be easier said than done.
Economist Susan Helper at Case Western University, said she believes it is possible — albeit expensive — to bring at least a majority of apparel manufacturing back to the U.S.
However, Helper said that it is not an issue that can be solved with tariffs alone.
“In order to compete or bring stuff back, you have to build up a new supply chain,” said Helper.
Margaret Bishop, supply chain expert at Parsons School of Design and the Fashion Institute of Technology, said she believes apparel manufacturing will not be restored anytime soon. The biggest problem? The lack of apparel factories.
“We have a few, but very few, and we don’t have any large-scale factories,” said Bishop.
There’s also the matter of workers to fill those factories. Since 1990, the number of employees in the apparel manufacturing industry has declined 91% from 983,600 in January 1990 to around 84,100 in March 2025.
In the U.S., many of those who still know industrial sewing are immigrants who have experience working in factories abroad, said Bishop. But the Trump administration is notoriously hostile to immigrants.
“If we have fewer immigrants or lose the immigrants we have, we’re losing that workforce,” said Bishop.
Many Americans who had that knowledge have long retired, said Marsha Dickson, chairperson of fashion and apparel studies at the University of Delaware.
“When production went overseas in the ‘80s, it was kind of the last generation of U.S.-based production managers,” said Dickson.
Training new workers in industrial sewing would be difficult due to how physical the role is and how low it pays. In 2023, sewing machine operators made a median annual wage of $33,400, lower than the national median annual wage of $42,220.
“Who in the U.S. really wants a job in the apparel industry, in a factory, sewing clothing?” said Dickson. “It’s very hard work. It’s very unreliable work.”
(The idea of Americans working in garment factories has recently become a meme on Chinese social media.)
And while automation has come to many different industries, sewing requires a finer touch.
“There still has not been anybody that has figured out how robots can pick up little pieces of fabric, put them together in exactly the right way and sew them together,” said Dickson.
Another factor? Raw materials, and additional factories to process those raw materials.
Sheep in the U.S. are often not bred for wool; the highest quality fibers tend to come from Australia and New Zealand. Flax in the country is produced for seed, not linen fibers. And while the U.S. is one of the largest exporters of raw cotton, it is also the largest importer of finished cotton products, like apparel and home textiles.
Plus, there’s still the matter of clothing trimmings.
“The snaps, the zips, the buttons, the thread — the majority of those raw materials inputs are imported,” said Dickson. “So not only would you have a higher wage for U.S. workers, you’d have import duties on the necessary raw materials. And so it’s going to further increase the price and make that clothing less attractive to today’s consumer.”
There are also other things to consider when it comes to textiles, such as different fabric types, prints and weights — think heavy winter knits versus linens for summer.
“You need textile mills producing lots of different fabrics, and that’s all siloed,” said Bishop. “You don’t typically produce knitted fabrics in a mill that also weaves woven fabrics and vice versa. And you don’t typically have both really sheer lightweight fabrics and heavyweight bottom weight fabrics like denims produced in the same mill for a variety of supply chain and production reasons.”
Standing up just one factory that could handle a part of the textile manufacturing process would take “billions of dollars,” said Bishop.
Policies that would help the apparel industry, Bishop said, would have to be a combination of no tariffs on raw materials, as well as tax, employment and training incentives. But that doesn’t solve every issue, such as massive consumer demand for quick, trendy clothing.
Bishop said it would be years before there would be enough factories to meet the American consumer tastes.
“For most brands, it’s about getting consumers to buy more frequently and to buy more per purchase,” said Bishop. “I think it’s going to be really tough to significantly change consumer behavior.”
Granted, Bishop said that consumer behavior might change out of necessity if purchasing clothing becomes less practical due to apparel price increases or increases in other staple goods.
“As prices go up, whether it’s prices in clothing or prices in food and automobiles and so forth, they’re simply not going to be able to afford as much,” said Bishop.